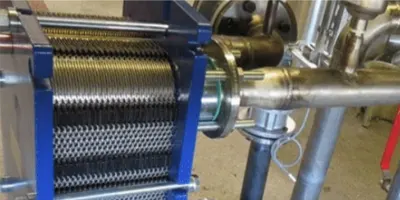
Heat exchanger installed at a Sun Chemical German facility replaced a cooling tower that was wasting heat and saved 470 MWh a year — a reduction of 98,700 kgCO2eq.
Recognizing that climate change is a social imperative and that our industry has a part to play in achieving a future where the worst effects of climate change are mitigated, Sun Chemical and the entire DIC Group, has pledged to reduce the greenhouse gas emissions of our manufacturing operations and to be carbon neutral by 2050.
Validated by the Science-Based Targets initiative, Sun Chemical is committed to: (1) reduce greenhouse gas emissions 27.5% by 2030 relative to base year 2019; (2) lower greenhouse gas emissions from capital goods, fuel- and energy-related activities, upstream transportation and distribution, waste generated in operations, and end-of-life treatment of sold products 13.5% by 2030 from base year 2019; and (3) work so that 80% of its suppliers by spend, covering purchased goods and services, will have science-based targets by 2027.
To achieve our operational goals, Sun Chemical uses what we call «the five Rs»—reuse, reduce, renew, recycle, and redesign—to guide our sustainability practices for our operations. This approach means that Sun Chemical will need to explore a variety of ways to decrease greenhouse gas-generating sources of energy, including:
This can be done by converting most of our electricity purchasing to green electricity and investing in photovoltaic arrays, windmills or other means.
Here are some examples of ways we’re working to achieve our 2030 and 2050 goals:
Heat exchanger installed at a Sun Chemical German facility replaced a cooling tower that was wasting heat and saved 470 MWh a year — a reduction of 98,700 kgCO2eq.
Solar panels installed at Sun Chemical’s Carlstadt, New Jersey site generated 871 MWh of power and reduced CO2 annually by over 1.3 million lbs (or over 600 metric tonnes).
Installation of distillation technology now recycles cleaning solvent, saving 10 kg of CO2 emissions for every gallon of solvent recycled.
Sun Chemical Polish manufacturing plant invested in a gas scrubber which treats over 7,000 cubic meters of air per hour, improving air quality and increasing production capacity.
Sun Chemical manufacturing plant in the United States invested in a tub washer, reducing energy usage by 130 kW per day.
A Sun Chemical Italian facility replaced mercury vapor lamps with LED lighting, saving 350 MWh per year.
A former mica mine area at Sun Chemical’s Hartwell, Georgia location was reclaimed to forma new lake for wildlife habitats.
Sun Chemical’s Muskegon, Michigan pigment site reduced natural gas usage by using the biogas from a municipal landfill to produce 85% of the plant’s steam requirements, as seen in PPCJ Magazine.